The steel industry, as a major contributor to global carbon emissions (accounting for 7.2%), plays a pivotal role in achieving the “dual carbon” goals. In recent years, technological innovations such as hydrogen-based metallurgy, electric arc furnace (EAF) short-process steelmaking, and carbon capture, utilization, and storage (CCUS) have driven the development of green steel. However, between 2024 and 2025, several landmark global green steel projects (e.g., thyssenkrupp in Germany and arcelormittal in France) faced stagnation due to technical bottlenecks, cost pressures, and insufficient industrial chain coordination. Even projects originally scheduled for commissioning in 2026-2027 have encountered slow progress, exposing deep-seated contradictions in the global industrialization of green steel.
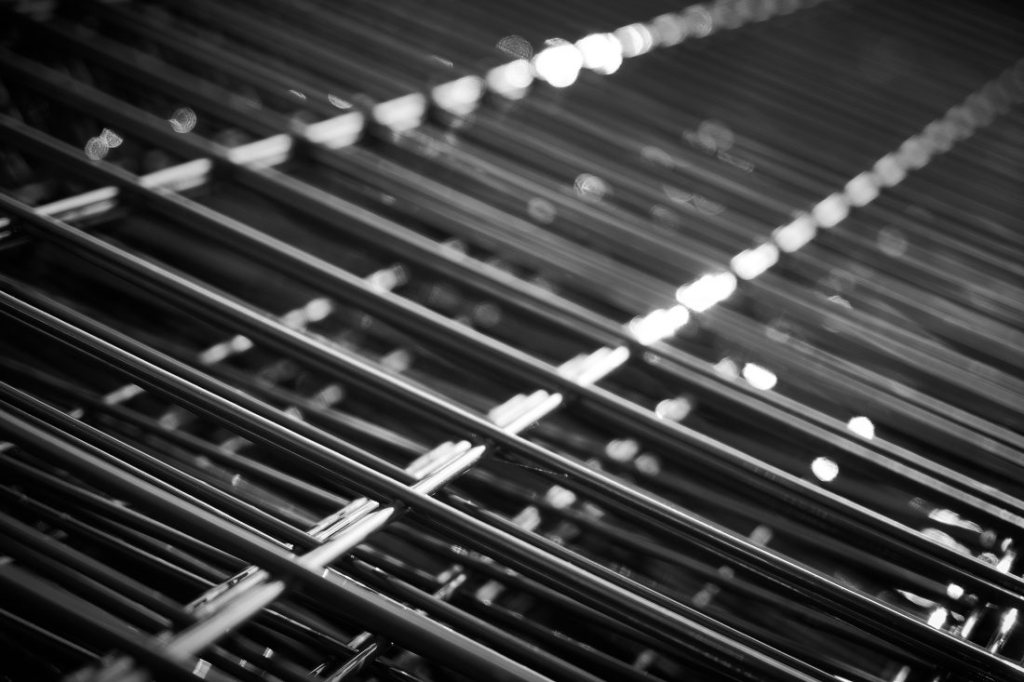
01.
Technical Bottlenecks in the Development of Green Steel
Scalability Challenges of Hydrogen Metallurgy. Hydrogen-Based Direct Reduction Ironmaking (H2-DRI), widely regarded as the cornerstone pathway for zero-carbon steel production, faces significant industrialization challenges due to fragmented green hydrogen supply chains and prohibitively high costs. For instance, the ThyssenKrupp Duisburg project in Germany—a flagship initiative—requires approximately 100,000 tonnes/year of green hydrogen. However, current production costs in Europe range from 3.74to3.74to11.7 per kilogram, far exceeding the economically viable threshold of €2/kg for large-scale adoption.
Hydrogen-based ironmaking (H2-DRI) critically depends on renewable energy supply, with the production of 100 million tons of green steel requiring approximately 2,000 GW of renewable electricity – equivalent to two-thirds of the current global renewable energy capacity. The process faces compounded cost pressures due to both the high energy intensity of electrolytic hydrogen production (~50 kWh/kg H₂) and the price volatility of renewable electricity.Moreover, the scaling-up of hydrogen-based reactors remains in the experimental phase, with significant technical hurdles yet to be overcome. Current reactor capacities are estimated to be only one-tenth that of conventional blast furnaces, further constraining large-scale industrial deployment.
Raw Material Constraints in EAF Short-Process Steelmaking. The electric arc furnace (EAF) process predominantly relies on scrap steel resources. However, the global scrap recycling rate remains at only 37% (18% in China), and inconsistent scrap quality restricts the production of high-grade steel products. According to data from the China Iron and Steel Association (CISA), in 2024, the production cost of EAF steel was 300–500 RMB/ton higher than that of basic oxygen furnace (BOF) steel, resulting in insufficient market competitiveness. To address this, policy measures such as time-of-use electricity pricing and direct renewable power supply are required to reduce energy costs.From a technical perspective, adopting ultra-high-power EAFs combined with scrap preheating can shorten the smelting cycle to 40 minutes and reduce power consumption to 300 kWh/ton, enhancing efficiency and cost-effectiveness.
Economic Viability Challenges of Carbon Capture Technology (CCUS). As a transitional decarbonization technology, CCUS currently faces substantial economic hurdles, with capture costs averaging $50/ton CO₂. However, downstream carbon storage and utilization pathways remain technologically immature for large-scale deployment. The International Energy Agency (IEA) estimates that the steel industry must achieve 55% emission reductions through CCUS to meet climate targets. Nevertheless, only 10% of global CCUS projects have reached commercial-scale operation as of 2024, highlighting significant gaps between theoretical potential and practical implementation.
02.
The Imbalance Between Economic Viability and Market Mechanisms
Inadequate Market Acceptance of Green Premiums.Green steel production incurs 20%-50% higher costs compared to conventional methods, yet downstream industries (e.g., automotive, construction) demonstrate lower-than-expected willingness to pay for low-carbon steel premiums. A notable case is Cleveland-Cliffs Inc. in the United States, which suspended a $500 million green steel project due to buyers’ refusal to cover the additional costs.
Fragmentation and Time-Lag Effects in Policy Support Systems. While the EU carbon price has reached historic highs (surpassing €100/ton CO₂), a persistent disconnect exists between subsidy mechanisms and technological advancement timelines. Illustrative of this mismatch, France’s €850 million subsidy to ArcelorMittal failed to resolve the critical path dependency in green hydrogen supply chain development. Concurrently, China’s inclusion of the steel sector in its national carbon market reveals systemic challenges, particularly in quota allocation mechanisms (lacking output-based benchmarking) and secondary market liquidity (with traded volumes covering <5% of allocated allowances in 2024).
Barriers from Sunk Costs in Conventional Production Capacity. The global steel industry faces significant decarbonization inertia due to 30-50 year investment cycles in traditional production assets, resulting in weak retrofit incentives. For instance, Nippon Steel’s hydrogen-injection technology for blast furnaces achieves merely 30% emission reductions, while requiring substantial capital expenditures of $200 per ton of capacity – a prohibitive cost that undermines the economic rationale for transition.
Economic Viability of CCUS. As a transitional technology, CCUS faces capture costs of ~$50/ton CO₂, yet storage and utilization remain immature. The IEA estimates that 55% of steel industry emissions must be cut via CCUS, but only 10% of global projects have reached commercialization.
03.
Lack of Industrial Synergy and Global Cooperation
Insufficient Upstream-Downstream Coordination. Steel decarbonization requires systemic alignment with mining and energy sectors, yet critical gaps persist in establishing scaled networks for low-carbon iron ore (e.g., direct reduced iron, DRI) and renewable electricity supply. The suspension of Australian hydrogen projects due to prohibitive green hydrogen costs (exceeding $5/kg H<sub>2</sub>) underscores the fragility of cross-industry synergies.
Conflicts Between International Standards and Trade Barriers. The absence of unified global standards for green steel certification has created significant trade tensions, particularly as the EU’s Carbon Border Adjustment Mechanism (CBAM) fails to account for the differential technological capacities of developing nations. While China has implemented ultra-low emission (ULE) retrofits, achieving compliance across 80% of production capacity has been delayed until 2025—further complicating international recognition efforts.
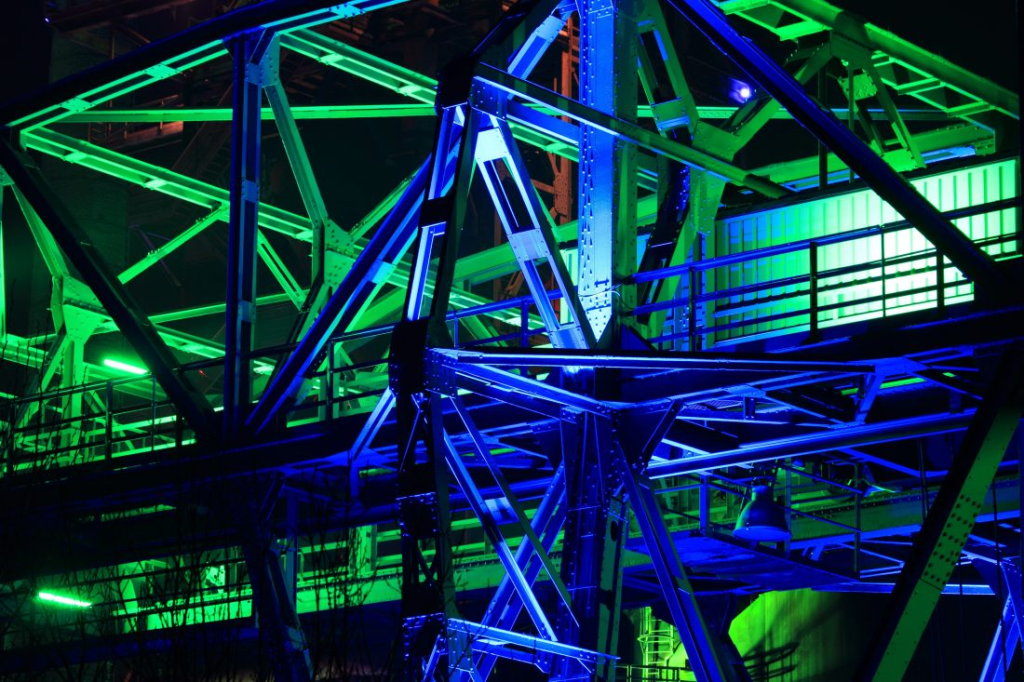
04
Breakthrough Pathways and Future Perspectives
Technological Innovation: From Discrete Breakthroughs to Systemic Integration. The path forward necessitates accelerating green hydrogen cost reduction through advanced technologies like proton exchange membrane (PEM) electrolyzers, targeting electrolysis efficiency exceeding 75% alongside gigawatt-scale production. Concurrently, hybrid metallurgical pathways—integrating hydrogen-based direct reduced iron (H2-DRI) with biomass energy while utilizing transitional fuels (e.g., natural gas, coke oven gas)—can mitigate reliance on pure green hydrogen during the scaling phase. This dual approach combines cutting-edge efficiency gains with pragmatic transition strategies to bridge technical and economic gaps in steel decarbonization.
Policy Restructuring: Establishing a Full Lifecycle Support System. The implementation of “carbon cost internalization” – integrating carbon emission costs into steel pricing mechanisms – represents a critical strategy for systemic decarbonization. China’s inclusion of the steel sector in its national carbon market serves as a pivotal initial step, though achieving fully functional market-based trading faces near-term challenges. Ultimately, this mechanism will fulfill its market-driven decarbonization objectives, transforming carbon reduction into an integral component of routine industrial operations. This approach aligns with the “polluter pays” principle while addressing the fundamental market failure of unpriced externalities in heavy industry.
Innovative Financial Instruments. The issuance of green bonds and other sustainable financial instruments has been instrumental in funding technological R&D, with numerous European financial institutions providing substantial transition financing for hydrogen-based metallurgy projects, including those by ThyssenKrupp, to support companies through the decarbonization transition. Ultimately, however, market-based mechanisms must prevail to ensure sustainable investment solutions.
Industrial Chain Collaboration: Forging a Green Steel Ecosystem. China Baowu’s Zhanjiang base exemplifies integrated hydrogen ecosystems by co-locating offshore wind-powered electrolysis with steel production, enabling on-site green hydrogen utilization. Meanwhile, HBIS Group pioneers long-distance hydrogen transmission through emerging pipeline networks. Complementing regional hydrogen clusters in Europe, the proposed European Hydrogen Bank is poised to play a pivotal role in securing hydrogen supply for metallurgical applications through market-based allocation mechanisms.
Scrap Steel Recycling System Upgrade. Blockchain-based Scrap Provenance Tracking for Electric Arc Furnace (EAF) Feedstock Quality Enhancement requires establishing standardized recycling networks, deploying intelligent scrap crushing and sorting technologies, and improving removal efficiency of deleterious elements (Cu, As, Pb, Zn) to meet stringent metallurgical purity specifications. This integrated approach aligns with ASTM E1919 standards for ferrous scrap quality while incorporating Industry 4.0 solutions like AI-powered LIBS (Laser-Induced Breakdown Spectroscopy) for real-time impurity detection and digital material passports for chain-of-custody documentation throughout the scrap value chain.
The challenges confronting green steel production are indisputable, yet they are inherently transient—a manifestation of the structural growing pains accompanying the paradigm shift in industrial civilization. This transition mirrors historical patterns of industrial transformation, wherein systemic breakthroughs have been contingent upon the tripartite interplay of technological advancement, policy reform, and market evolution.
Present obstacles—such as the prohibitively high costs of green hydrogen and fragmentation across the supply chain—underscore the sector’s interim struggles. However, over the coming decade, the global steel industry is poised to leverage a synergistic framework of technological innovation, collaborative governance, and market-driven mechanisms to transmute these sustainability challenges into long-term opportunities for decarbonization and resilient growth.